壓力傳感器在鋰電行業的應用十分廣泛,涵蓋了從原材料處理到成品電池檢測等多個環節。以下是一些具體的應用場景:
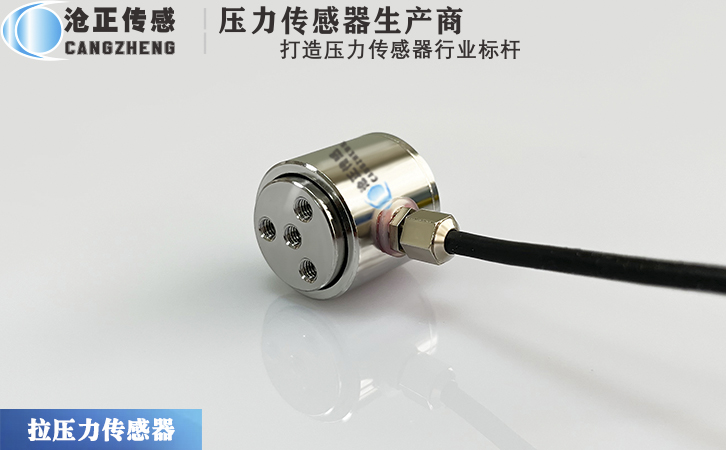
攪拌環節:在鋰電池生產的攪拌工序中,可在攪拌桶底部安裝稱重模塊(壓力傳感器),用于監控配方比例的注入情況,確保物料的精確投放,保障安全生產,避免因原料比例不準確影響電池性能。
涂布環節:物料生產完成進行涂布時,通過涂布熔噴頭噴出的壓強來確保覆料均勻。力傳感器可實時監測噴頭的壓力,保證涂布的一致性和穩定性。
碾壓環節:加裝壓力傳感器能夠監控碾壓機的壓力波動,確保碾壓程度符合要求,使鋰電池極片的厚度和密度達到標準,對電池的性能和容量有重要影響。
分切(輥壓)和卷繞(疊片)環節:張力傳感器可通過監測過輥張力的變化,即張力的波動情況,來確保料過輥的程度,達到對這兩個環節的監測目的,保障極片在分切和卷繞過程中的質量。
冷熱壓環節:將卷繞后的電芯進行壓合成型時,力傳感器可用于監控壓力,使電芯獲得需求的密度以及厚度,保證電池的形狀和結構穩定性。
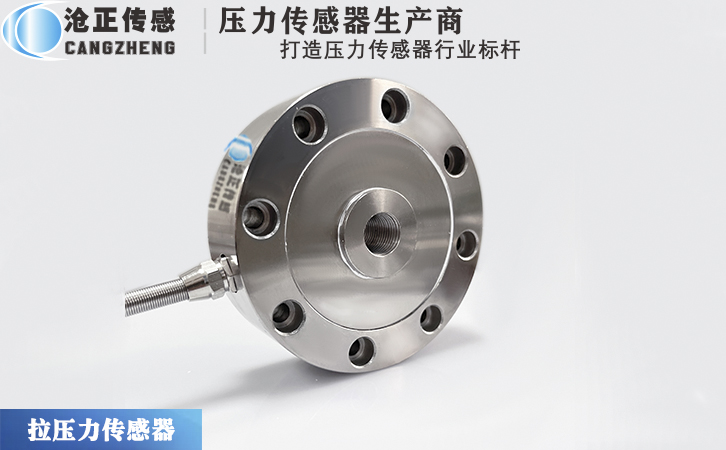
入殼環節:通過壓力監控可以檢測入殼過程是否異常,如是否存在卡殼、碰撞等情況,避免對電芯造成損壞。
焊接環節:對焊接容口進行壓力監控,保證焊接的程度和質量,防止虛焊、漏焊等問題,確保電池的電氣連接可靠性。
注液環節:在注液過程中,通過力傳感器測量加入電解液前后電池的重量變化,從而確定實際注入電解質的重量,精確控制注液量,對電池的性能和安全性至關重要。
成品電池檢測:可以檢測電池在不同使用狀態下(如充電、放電、靜置等)所受到的力的情況,分析電池的機械性能和結構穩定性。例如,檢測電池在充放電過程中的膨脹力,評估電池的安全性和壽命;對電池進行擠壓、沖擊等測試時,力傳感器可實時反饋受力數據,判斷電池是否能夠承受相應的外力作用而不損壞,從而篩選出不合格產品。
零部件檢測:用于檢測鋰電池的各種零部件,如電極片、隔膜、外殼等的力學性能。例如,檢測電極片的抗拉強度、隔膜的抗穿刺強度等,確保零部件的質量符合要求,從源頭上保障鋰電池的質量和性能。
過充過放監測:在電池過充或過放過程中,內部會產生較大的壓力變化。通過力傳感器監測電池內部的壓力,可以及時發現過充過放情況,避免電池因過度充放電而損壞甚至引發安全事故。
熱失控預警:當電池發生熱失控時,會伴隨有氣體產生、壓力急劇上升等現象。力傳感器可用于檢測電池在這些情況下所受到的力,評估電池的抗沖擊和抗振動能力,為電池的包裝、固定和防護設計提供依據,確保電池在不同環境下的安全使用。
材料研究:在研發新型鋰電池材料時,力傳感器可用于測量材料在不同條件下的力學性能,如彈性模量、屈服強度等,為材料的選擇和優化提供數據支持。例如,研究電極材料在充放電過程中的膨脹收縮特性,有助于開發出更穩定、性能更優的電極材料。
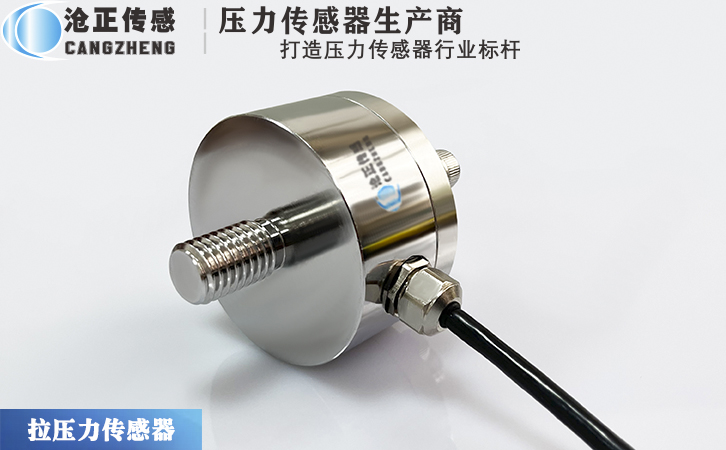
結構設計優化:通過在電池結構上安裝力傳感器,可以獲取電池在各種工況下的受力分布和變形情況。依據這些數據對電池的結構進行優化設計,提高電池的整體性能和可靠性。例如,優化電池外殼的結構,使其能夠更好地承受內部壓力和外部沖擊;調整電池內部組件的布局和連接方式,降低應力集中,延長電池的使用壽命。
壓力傳感器在鋰電行業的應用不僅提高了生產效率和產品質量,還為電池的安全性和可靠性提供了有力保障。隨著技術的不斷進步和成本的進一步降低,壓力傳感器在鋰電行業的應用前景將更加廣闊。